Failed oxygen valve at mining complex in Arizona
Our experts go above and beyond the call of duty to find the products you need, FAST.
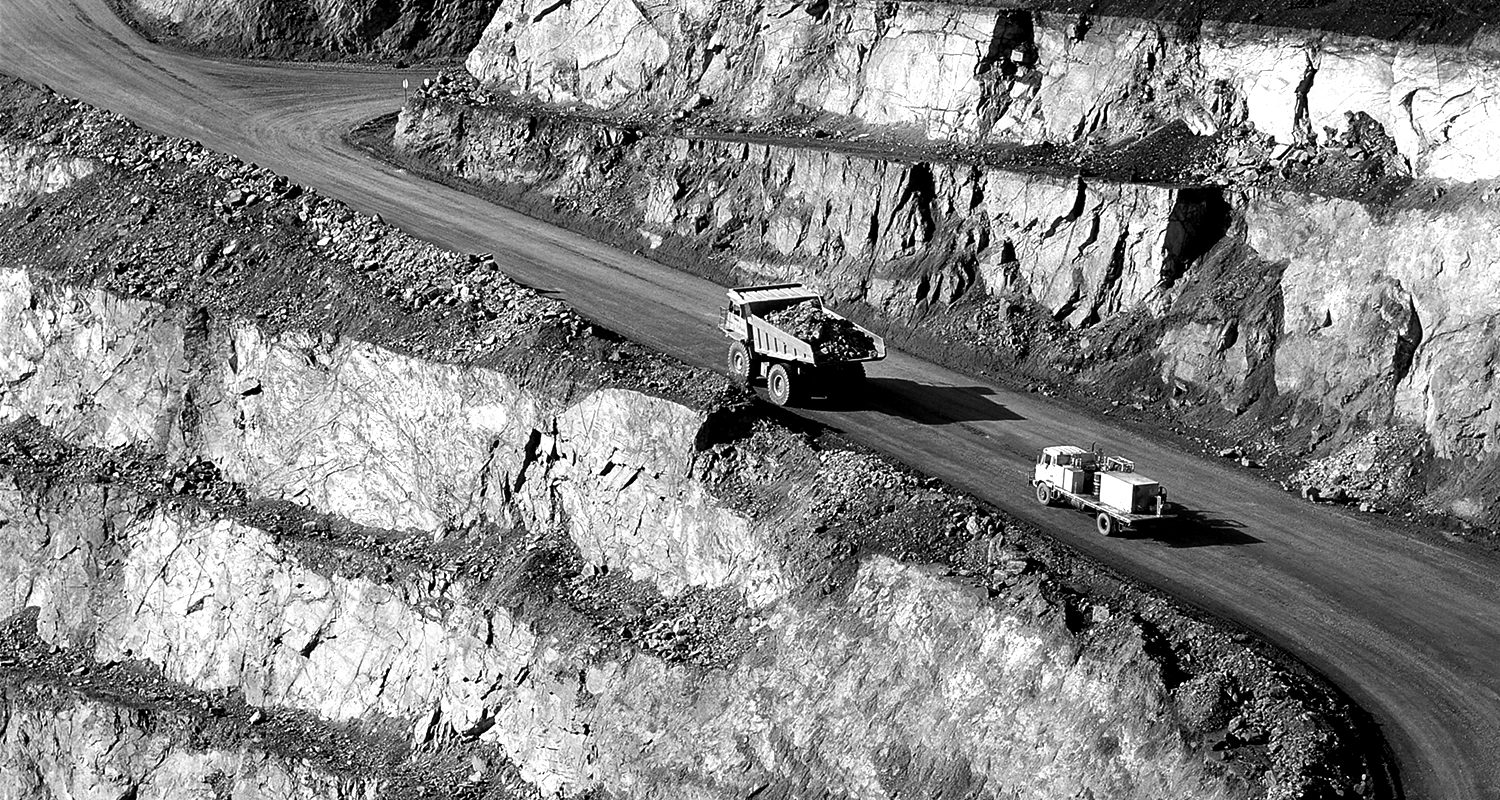
When an unexpected product failure slows operations to a crawl, facilities need a partner they can trust. A partner who will do whatever it takes to deliver a replacement quickly and get operations back to action.
Time is money.
Ferguson Industrial understands the urgency that follows product failures. That is why we’re willing to do whatever it takes to get our customers up and running again. When an oxygen valve failed in a vessel at an open pit mining complex in Arizona, the facility knew we could provide a quality, quickly-sourced solution.
The oxygen valve failure created a critical safety issue for the mining complex. Consequently, operations were forced to slow down. Unfortunately, the customer was unable to provide exact product details for the valve, however, our experts were able to identify the product after viewing a few pictures and some service conditions: a 1″, 300#, stainless steel, full-port, split-body, automated, metal-seated ball valve.
We quickly realized that sourcing and delivering an exact replacement would take 10-12 weeks. Right away, we knew this timeframe was unacceptable for their current rate of operation. That is why our team jumped into action. We worked tirelessly to qualify the customer’s needs and find an alternative valve. As a result, we located an equivalent product from our Approved Manufacturers List. Then we built the valve package and mount tested it at our Valve Automation Center in Chicago.
Within 72 hours, our customer had the entire assembly mounted and operational on site.
Our knowledgeable associates, quick response, and project ownership were crucial to reducing lead times, minimizing expensive downtime, and re-establishing a safe operating environment for the mine complex team.
View Similiar Case Studies
Our Automated Supply Program (ASP)—an advanced, indirect material supply chain software—and our proven processes to control their MRO indirect spending reduced the total cost of ownership by 24.2% in the first year post-integration.
Our associates identified an opportunity to use our online Automated Valve Configuration Tool to build out exactly what the customer needed. In less than 15 minutes, our flow control experts were able to walk the customer through the process of configuring an FNW® automated ball valve package.
Expert technical assessment, material selection, and supply of Polypropylene at a quartz processing facility in North Carolina.