Industrial Valve Experts Discover Critical Error in Automated Isolation Valve Installation
Comprehensive product knowledge and an unshakable commitment to service lay the framework for swift, dynamic problem solving.
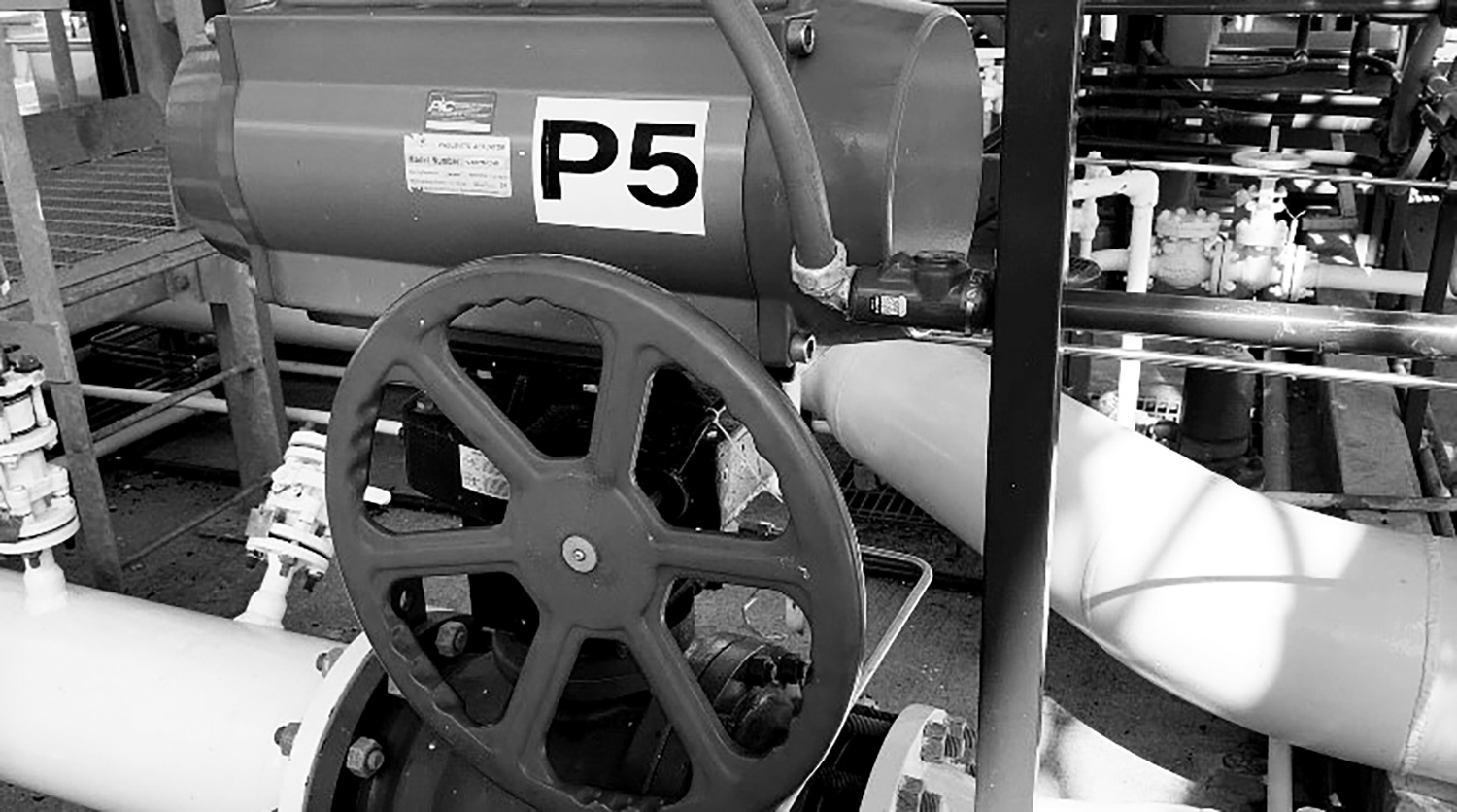
Part of the purchasing process is an implicit contract. To explain, a customer buys products from their supplier with the understanding that the products will work at or above expectations. When a product fails to meet this standard, a true supply partner goes out of their way to resolve the matter.
When a customer experiences failure with a brand-new automated isolation valve, Ferguson Industrial provides a step-by-step fix.
After supplying four 10-inch automated isolation valves to an oil and gas pipeline storage company, a problem was soon discovered. The four valves were not achieving complete open and closed positions as designated in the control logic.
In response, our valve experts conducted an on-site visit to troubleshoot the valves. After careful inspection, we discovered a critical sticker had been left off the gear operators. The stickers indicated a precise procedure for the operation of the gear operators to avoid catastrophic failure. Without these stickers, the customer had accidentally caused a failure. Consequently, it shut down the normal valve and actuator operation.
Due to the COVID-19 pandemic, we couldn’t send a team to replace the failed gear operators ourselves. Instead, we arranged for new gear operators to be delivered at no charge. In addition, we produced a step-by-step video demonstrating the proper installation of the new equipment.
Despite not having our full team on site, the customer completed the automated isolation valve changeout successfully and with minimal downtime.
View Similiar Case Studies
Our Automated Supply Program (ASP)—an advanced, indirect material supply chain software—and our proven processes to control their MRO indirect spending reduced the total cost of ownership by 24.2% in the first year post-integration.
Our associates identified an opportunity to use our online Automated Valve Configuration Tool to build out exactly what the customer needed. In less than 15 minutes, our flow control experts were able to walk the customer through the process of configuring an FNW® automated ball valve package.
Expert technical assessment, material selection, and supply of Polypropylene at a quartz processing facility in North Carolina.