Industrial PVF Delivery to Ohio Valley fertilizer customer saves time and reduces costs
Maximize our capabilities to realize cost savings and reduce lead times.
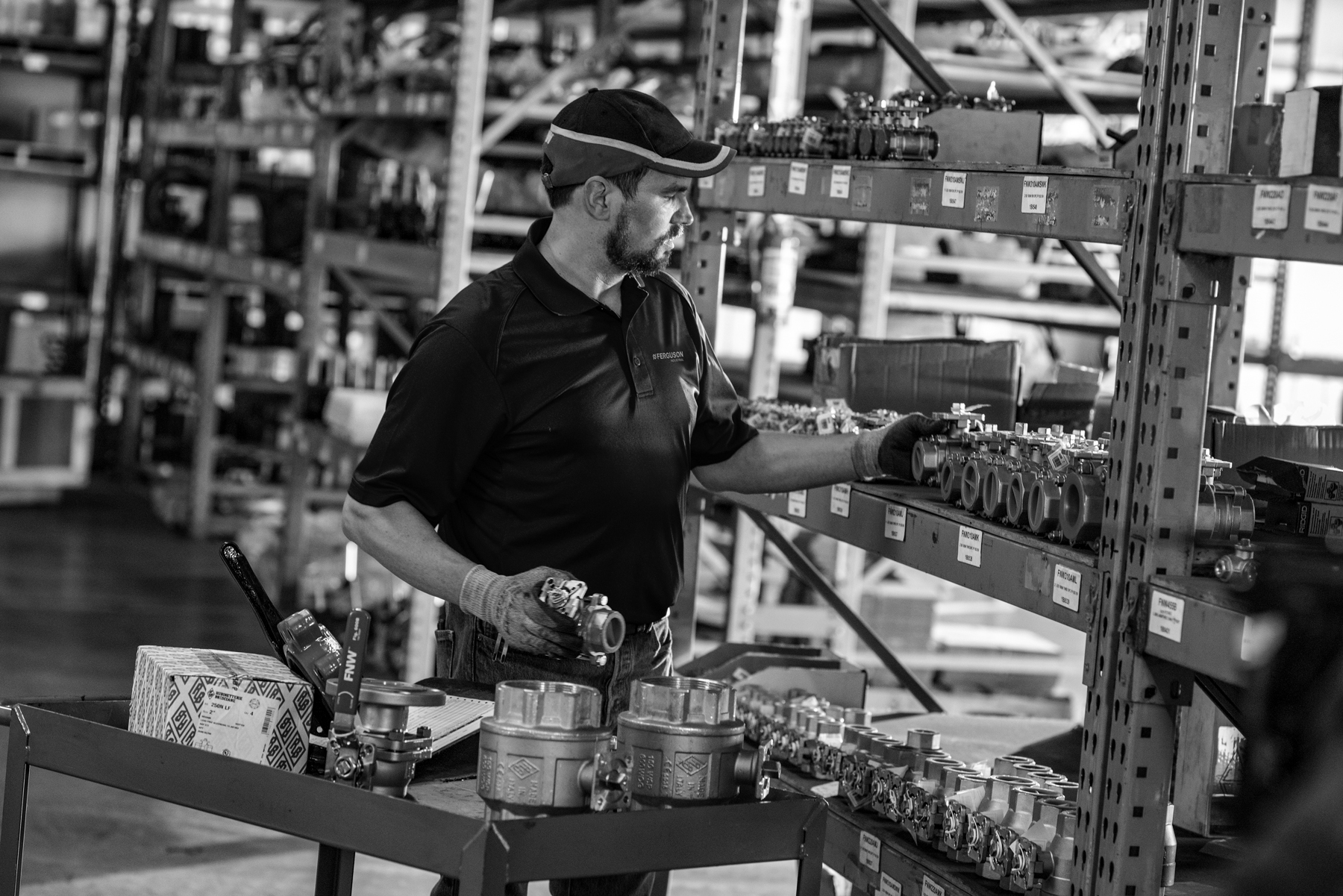
Fast-paced, large-scale capital projects require leaders and problem solvers, not just order-takers and product peddlers. When it comes to planning and execution, you need a capable partner—one with vast reach and the ability to work with your needs at the local level. An industrial partner that provides competitive pricing, industry expertise, reduced lead times, increased cost savings, and fast industrial PVF delivery.
Our associates are ready, willing, and able to contribute to your project’s success. We’re not just sales associates, we’re partners. We go beyond listening and instead communicate with our customers to fully understand the details and specifications. We’re able to scale these capabilities at a national level, but we pride ourselves on empowering your success at a local level as well. After all, our national footprint means nothing if it can’t support the very communities it walks through.
Delivering PVF Products On Time and Under Budget for Crucial Maintenance Work and Capital Projects
When one Ohio Valley fertilizer customer and their contractor faced tight time and budget constraints for crucial maintenance work and capital projects, they trusted us to deliver the necessary PVF on time and under budget. Not only were we able to expedite this customer’s orders by utilizing our local distribution center and truck drivers, but we also contributed to huge cost savings. This was accomplished by avoiding freight fees and replacement costs. In total, by partnering with Ferguson Industrial and taking advantage of our logistics network, our customer saved more than $500,000 during the three-month project.
When you work with us, you can trust that we’ll do everything in our power—turn over every stone, make every call, deliver every product no matter the roadblock—to be the partner your project deserves.
View Similiar Case Studies
Our Automated Supply Program (ASP)—an advanced, indirect material supply chain software—and our proven processes to control their MRO indirect spending reduced the total cost of ownership by 24.2% in the first year post-integration.
Our associates identified an opportunity to use our online Automated Valve Configuration Tool to build out exactly what the customer needed. In less than 15 minutes, our flow control experts were able to walk the customer through the process of configuring an FNW® automated ball valve package.
Expert technical assessment, material selection, and supply of Polypropylene at a quartz processing facility in North Carolina.